Est. reading time: 5 min
Managing inventory efficiently is crucial for businesses to avoid both overstocking and stockouts. The Reorder Point (ROP) calculator helps businesses determine the optimal time to reorder stock based on their inventory levels, ensuring they have just enough inventory to meet demand without tying up excess capital.
Also try:
Table of Contents
- Word Definitions
- What is a Reorder Point?
- How to Calculate the Reorder Point
- Examples of Reorder Point Calculations
- Frequently Asked Questions
- Further Reading
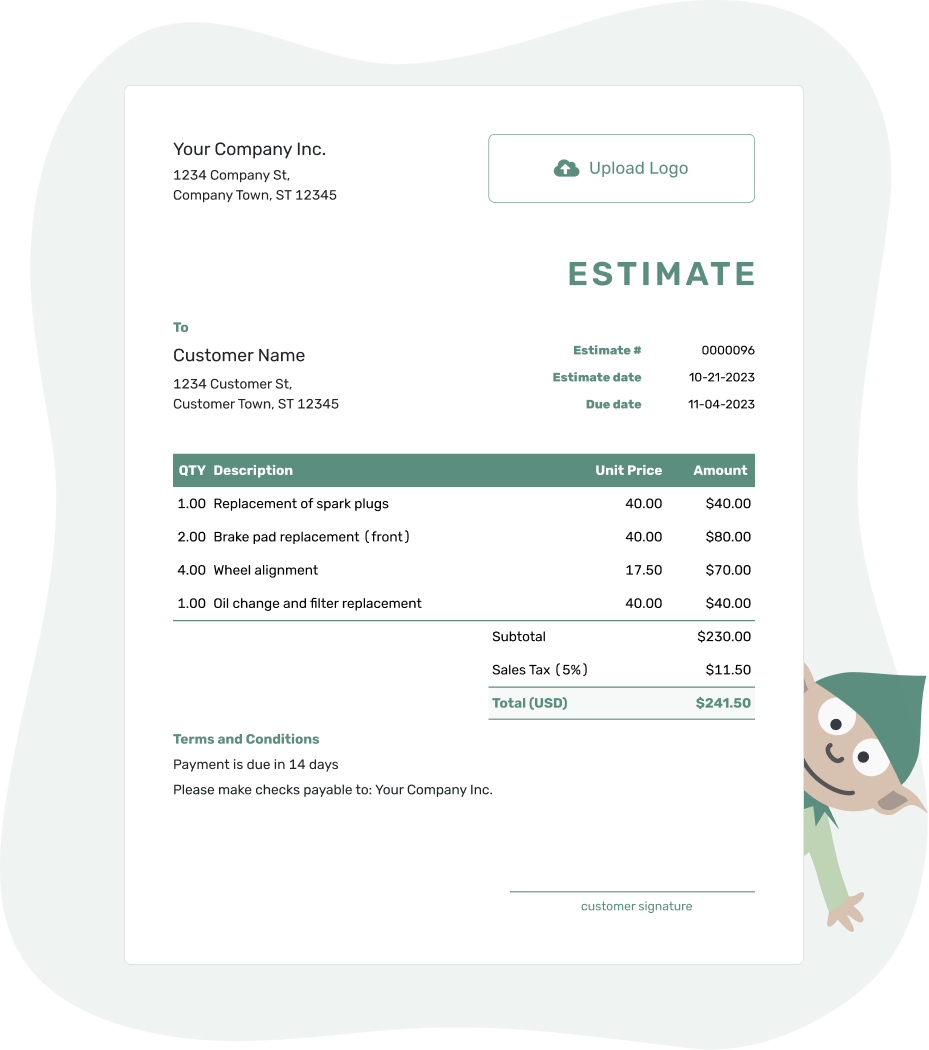
- PDF, Email or Print
- Convert to Invoice
- See when your estimate has been opened
- Get notified when your estimate is accepted
Word Definitions
-
Reorder Point (ROP):
The inventory level at which a new order needs to be placed to replenish stock, ensuring no stockouts occur before the new inventory arrives. -
Safety Stock:
Extra inventory kept on hand to protect against fluctuations in demand or supply and to prevent stockouts. -
Lead Time:
The time it takes from placing an order to when it is received and ready for use or sale. -
Average Daily Sales:
The average number of units sold per day, calculated over a specified period to smooth out fluctuations.
What is a Reorder Point?
The reorder point is a critical threshold in inventory management that triggers the action to reorder stock. It is calculated to ensure that you have enough stock on hand until new stock arrives, factoring in lead times and variability in demand and supply. This calculation is essential for maintaining smooth operations and avoiding inventory shortages or excesses.
How to Calculate the Reorder Point
The basic formula for calculating a reorder point (ROP) is:
ROP = | (Average Daily Sales × Lead Time) + Safety Stock |
Accurately calculating reorder points requires understanding and determining several key values specific to your business operations. Below, we explain how to determine safety stock, lead time, and average daily sales for your business.
Determining Safety Stock
Safety stock acts as a protective buffer against variability in demand and supply chain disruptions. To calculate safety stock, you need to assess the variability in both lead time and demand during the lead time. Use historical data to calculate the standard deviation of lead time and demand. Then, apply the formula:
Safety Stock = Z × σLT × Davg |
Where Z is the Z-score based on the desired service level, σLT (sigma) is the standard deviation of lead time, and Davg is the average demand.
Determining Lead Time
Lead time is the period between placing an order and receiving the stock. To determine accurate lead time, track the actual time it takes for several orders from placement to delivery. Calculate the average of these times to get a reliable lead time estimate. Consider communicating regularly with your suppliers to get updates on any factors that might affect lead time, such as changes in manufacturing processes or shipping delays.
Determining Average Daily Sales
Average daily sales are calculated by dividing the total sales of a product over a specified period by the number of days in that period. Choose a timeframe that reflects your typical sales cycle without being overly influenced by seasonal spikes or unusual events. For more accurate forecasting, segment sales data by market or channel if your business operates across multiple platforms.
Examples of Reorder Point Calculations
To better understand how to apply the Reorder Point (ROP) formula in different scenarios, consider the following examples:
Example 1: Small Retail Business
A small retail store specializing in boutique clothing calculates their reorder point for a popular dress style. They have determined the following:
- Average Daily Sales: 5 dresses
- Lead Time: 10 days
- Safety Stock: 15 dresses
Using the ROP formula:
ROP = | = (5 × 10) + 15 = 65 |
The store should reorder dresses when their inventory reaches 65 units to ensure they have enough stock to cover sales during the lead time and any unforeseen demand spikes.
Example 2: Electronics Distributor
An electronics distributor needs to calculate the reorder point for a specific type of battery. Their data includes:
- Average Daily Sales: 20 batteries
- Lead Time: 5 days
- Safety Stock: 40 batteries
Applying the reorder point formula:
ROP = | = (20 × 5) + 40 = 140 |
Therefore, the distributor should initiate a new order when their stock level falls to 140 batteries to maintain continuous availability and meet customer demand.
Frequently Asked Questions
-
What is a reorder point?
A reorder point is the specific stock level at which an order must be placed to replenish inventory, ensuring no stockout occurs while waiting for the order to be fulfilled.
-
How do you calculate a reorder point?
Calculate the reorder point by multiplying the average daily usage by the lead time and then adding the safety stock.
-
Why is safety stock important in calculating reorder points?
Safety stock is crucial as it acts as a buffer against fluctuations in demand and supply. It ensures that even if deliveries are delayed or demand unexpectedly increases, the business can continue to operate without running out of stock.
-
How does lead time impact the reorder point calculation?
Lead time directly affects when you need to reorder stock. A longer lead time increases the reorder point because you need to order sooner to account for the longer waiting period. This ensures that you do not run out of stock before your new order arrives.
-
Can reorder points change over time?
Yes, reorder points can and should be adjusted over time as sales patterns and lead times evolve. Seasonal changes, market trends, and supplier reliability can all influence the optimal reorder point, making it important to regularly review and adjust your calculations.
-
What is the difference between reorder point and safety stock?
Reorder point (ROP) is the inventory level that triggers a replenishment order, whereas safety stock is additional inventory held to mitigate the risk of stockouts due to unexpected increases in demand or delays in supply.
-
What are the effects of an inaccurate reorder point?
An inaccurate reorder point can lead to overstocking, which ties up capital in excess inventory, or understocking, which can result in missed sales opportunities and dissatisfied customers due to stockouts.
-
How can businesses optimize their reorder point?
Businesses can optimize their reorder point by regularly reviewing their sales data, adjusting for seasonal variations, improving forecast accuracy, and closely monitoring supply chain dynamics to adapt to any changes in lead times or demand patterns.
-
What impact does technology have on managing reorder points?
Technology, especially inventory management systems, can significantly enhance the accuracy of reorder point calculations by automating data analysis and providing real-time inventory tracking, which helps in making timely and informed replenishment decisions.
-
How do businesses manage reorder points across multiple locations?
Managing reorder points across multiple locations involves centralized monitoring and localized adjustments. Each location's reorder point may vary based on local demand patterns, supply chain logistics, and storage capabilities, necessitating tailored strategies to ensure optimal inventory levels at each site.
Further Reading
To deepen your understanding of inventory management and the strategic application of reorder points, explore the following resources:
- APICS for Supply Chain Management - Provides extensive training and certification in supply chain management, including best practices in inventory management.
- Harvard Business Review - Operations - Offers articles and insights from leading experts on operations management and efficiency improvements.
- Council of Supply Chain Management Professionals (CSCMP) - A global association providing networking, career development, and educational opportunities in supply chain management.
- Supply Chain Management Review - Publishes articles, case studies, and white papers that focus on various aspects of supply chain management.
- INFORMS - The Institute for Operations Research and the Management Sciences - Offers resources and research covering a broad range of topics in operations research and analytics.
These resources provide valuable insights and guidance that can help both individuals and businesses better understand and manage their inventory systems.